Ce topic à pour but de vous faire partager les découvertes sur un sujet passionnant.
un peu d'historique
L'années dernières, fructueuse en découvertes intéressantes ( voir mes autres fils de discussion) j'ai du faire des réparations de pierre. après un premier essais, je me suis dis que je ne devais pas être le seul a penser à refaire des pierres avec liant et agrégat. J'ai donc cherché et suis tombé surRêve de pierre qui m'a donnée de précieuses informations sur les méthodes à utiliser Merci pour tout.
Quelque essais supplémentaires plus loin, à force de fréquenter de très belle pierre, je suis devenu assez déçu par l'aspect qui me semble beaucoup trop éloigné de la vraie pierre tant au touché qu'en aspect. Bref trop ciment, .
J'ai donc poursuivi mes recherche et suis arrivé sur le site de
Institut Géopolymère avec la théorie stupéfiante sur la construction des pyramides de J Davidovits. .
Au delà de ces pyramides, qui ne sont pas le sujet, j'ai découvert comment faire n'importe quelle pierre sans ciment portland, ni chaux et surtout avec une similitude qui trompe l'oeil le plus avertis.
Ma première expérience a été un boule d'argile mélangé à de la soude, mélange qui à ma grande surprise est devenue un cailloux dans les jours qui ont suivi.
Je me suis donc penché sur la question et j'ai découvert que cette méthode ancestrale faisait en fait partie des recherches sur les matériaux de pointes : des centaines de labo font des études, des expériance publient des brevet, des méthodes etc.
La plus grande difficulté a été de sortir de tous cette masse d'information la solution à mon problème.
J'ai essayé plusieurs fois croyant avoir enfin compris avant d'arriver à un résultat très acceptable.
Concretement
Enfin je suis arrivé ( enfin je pense) à une formulation donnant satisfaction:
85 à 90 % de calcaire
10 à 15 % d'argile kaolinique,éventuellement calciné, +
1/3 du poid d'argile en silicate silicate de soude +
1/12 du poids d'argile en soude caustique titré à 9ppm +
un minimum d'eau additionnelle ( un superplastifiant est le bienvenu) = réaction chimique qui produit une pierre identique à la pierre naturelle.
un peu de la chaleur de l'éte la réaction chimique est accélérée par la température
Le mélange obtenu est très très collant.
Un temps d'utilisation théoriquement réduit ( la prise peut se faire dans l'heure voir plus vite si la température est correct mais est aussi fonction du volumes .
le séchage ne doit pas être trop rapide la réaction chimique consomme de l'eau .
La dureté maxi est obtenue après séchage définitif Mais juste après démoulage, de quelques heures à plusieurs jours suivant le volume et la formulation la surface est suffisament meuble pour les finitions, de même en cas de fracture au démoulage la réparation possible juste en remouillant la matière ( possible tant que c'est suffisament humide).
J'ai actuellement quelque pb de fissuration, du probablement à un taux de silicium qui doit être assez haut mais aussi à cause d'inserts qui bloquent le retrait.
.
La pierre finie malgrès un aspect identique à une pierre normale est néanmoins beaucoup plus dur ( quasiment inpossible à rayer avec un couteau).
Voila voilà,
personnelement je n'utiliserai plus de ciment portland pour faire des pierres.
il est tard ce soir mais je vous promet d'extraire des docs ( la plupart en anglais) et de vous faire profiter de mes avancés sur le sujet
en attendant quelques photos des essais et pierres que je suis en train de faire pour un puits:
moulage de pierre Lien vers documents, publication, synthèse et autres
à venir
Réponses
Bravo pour ce sujet très intéressant et pour la présentation de vos expérimentations.
On voit un peu mieux grâce à vous comment un simple mouleur amateur que je suis pourrait appliquer chez lui ce que les spécialistes des géopolymères mettent tant d'ardeur à rendre compliqué en apparence.
Lien directe vers : L'invention et la technique de la pierre par geopolymer.org
Une question concernant les matériaux de base : Trouve t-on facilement, et où le trouvez-vous vous, de l'argile kaolinique ?
Merci
Merlin
Sinon pour l'argile on la trouve chez les grossistes de poterie ( solargil) , c'est blanc et le cout est de 0,95 au kg , idem pour le silicate de soude, et la soude en perle se trouve en grande surface pas chez casto ou c'est 2 fois plus cher. Le cholrure de magnésium chez les grossistes de produit agricole
Le cout final doit être équivalent à chaux + portland.
Il y a d'autre méthode, que je n'ai pas encore expérimenté, déjà utilisée par les entreprisee qui font des crépis chaux, mais dont ils ne connaissent pas le potentiel, c'est le mortier romain à base de chaux aérienne et de pouzzolane. Ces mortiers, bien fait peuvent durer des millier d'années. Sujet à creuser.
Il pourrait éviter d'utiliser le ciment portland et tous ses inconvénients.
En fait la technique du géopolymère, bien que pluri-millénaire en est à ses débuts et le but de l'institut est de rassembler, d'unifier, de compiler les recherches, d'étudier l'archéologie, Egyptien, Rome, Incas, etc , d'une part pour comprendre et d'autre part de rendre compréhensible et surtout applicable à grande échelle.
Ce n'est pas chose aisée, surtout en France avec le carcan de certaines normes, Mais comme cette technique réduit la pollution de l'ordre de 90%, utilise les résidus d'autres industrie, acier , électricité , que ce sont des liant très stable dans le temps, utile pour faire disparaître à jamais les polluants , les pouvoirs public de tous les pays sont très intéressés pour une évolution rapide et dans quelque années nous pouvons être sur qu'on nous vendra en grande surface des matériaux de ce type.
http://gpc.latech.edu/basis.htm/]information de base en anglais
en gros:
citation de l'article
Une pâte de ciment durcie faite de cendre volante sans ciment Portland. Il a une plus grande resistance à la compression, à la traction, plus dur,une porosité et perméabilité plus faible et une très bonne résistance à l'attaque chimique comparée avec le ciment de Portland ordinaire (OPC) le béton. Il peut utiliser les dechets d'autre processus industriel , limitant ainsi la mise en décharge décharge et promouvant la durabilité et enfin comparé avec le ciment de Portland, il permet de réduire de 90 % l'émission de dioxyde de carbone.
En pratique
Une solution d'hydroxyde de sodium et hydroxyde de potassium (des déchets des industries chimiques et pétrochimiques) doit être préparée séparément, ajoutée ensuite au silicate de sodium commercial liquide; cette solution peut alors être ajoutée à la cendre volante en poudre (le déchet de la combustion de charbon et bio de carburant) dans la même façon que l'eau est ajoutée pour le ciment de Portland. + =
Cure :
Une différence importante entre geopolymer et le ciment de Portland est que la réaction geopolymerization exige la demande un peu de chaleur ( la réaction se fait néanmoins à basse température mais moins vite)
La mise en températures s'est étendue entre 60 et 90 C selon les propriétés de la cendre volante utilisée.
Dans le laboratoire, des fours peuvent être utilisés ce qui est impossible en grandeur nature . des recherche sont faite pour diminuer cette nécessité.
BasicsRuston, la Louisiane, les USA
--------------------------------------------------------------------------------
Université de Technologie de la Louisiane - École d'ingénieurs et Science Ruston, la Louisiane, les USA, 71270
MAis une formule simple sans silicate de soude et peu d'argile convient très bien pour un usage intérieur.
Pour un usage extérieur il est impératif que le taux de silicium amené par le silicate et la quantité de liant total , soit suffisament haut pour avoir une résistance aux intempéries satisfaisante.
Cette résistance sera aussi fonction de l'agrégat utilisé, si naturellement le calcaire utilisé a tendance à se delitter alors la pierre final aura la même tendance
Vous pouvez utiliser du sable, de l'eau salé, faire des strates de couleur et composition différente, rajouter des couches si besoin, faire des réparations etc...
( j'essaierai quand même d'en sortir les éléments essentiel)
un article très technique qui explique les différents mecanisme qui se mettent en place lors de la géopolymerisation
s
Geopolymer technology: the current state of the art
GEOPOLYMER STONE FOR BUILDING AND DECORATION AND METHOD FOR OBTAINING SAME
patent n° WIPO Patent Application WO/2003/040054
le lien original est ici
Si vous avez la patience de lire,
Pierre géopolymèrique pour la construction et la décoration, et procédé d'obtention.
Description: La présente invention concerne un nouveau type de pierre reconstituée destinée à la construction et la décoration. Cette pierre reconstituée est appelée pierre géopolymèrique car le liant d'agglomération est à base de géopolymère minéral, constitué d'alumino- silicates alcalins, plus connus sous l'appellation de poly (sialate), poly (sialate-siloxo) et/ou poly (sialate-disiloxo).
Techniques antérieures.
Les pierres reconstituées sont dans l'art antérieur fabriquées en agglomérant des charges minérales soit avec des liants organiques, soit avec des liants hydrauliques à base de chaux et de ciment Portland. Les pierres faites avec des liants organiques ne peuvent pas tre destinées à un usage extérieur car il est connu que la matrice en résine organique ne résiste pas aux rayonnements UV et IR. On trouve ce type de pierre reconstituée essentiellement sous forme de dalles de « marbre artificiel », à l'intérieur des bâtiments. Les pierres reconstituées à l'aide de liants hydrauliques sont stables aux UV et IR et sont utilisées à l'extérieur, mais leur aspect décoratif est relativement médiocre. Mais, étant constituées de matrices sensibles à l'attaque chimique des acides, ces pierres, en général à base de calcaire, sont très rapidement attaquées par la pollution atmosphérique.
Les liants à base de géopolymère minéral, constitué d'alumino-silicates alcalins, plus connus sous l'appellation de poly (sialate), poly (sialate-siloxo) et/ou poly (sialate- disiloxo), n'ont pas les défauts présentés par les liants organiques et les liants hydrauliques traditionnels. Ils sont stables aux UV et IR, et sont très résistants aux acides.
Le terme poly (sialate) a été proposé pour désigner les géopolymères alumino- silicates. Le réseau sialate est constitué par des tétraèdres Si04 et A104 alternativement liés par des atomes d'oxygène. Les cations (Na+, K+, Ca++, H30+) présents dans les cavités structurales du poly (sialate) équilibrent la charge négative de AI 3+ en coordination (IV). La formule empirique des Polysialates est : Mnf- (Si02).,-A102n, wH20, avec M représentant le cation K, Na ou Ca et « n » le degré de polymérisation ; « z » est égal à l, 2,3 ou plus, jusque 32. Les polymères à réseau tridimensionnel (3D) sont de type :
Poly (sialate) M"- (-Si-O-Al-O-) , M-PS Si : Al= 1 : 1 Poly (sialate-siloxo) Mn-(Si-O-Al-O-Si-O-) n M-PSS Si : AI=2 : 1 Poly (sialate-disiloxo) M"- (Si-O-AI-O-Si-O-Si-O-) , M-PSDS Si : AI=3 : 1 Les géopolymères de type poly (sialate), poly (sialate-siloxo) et/ou poly (sialate- disiloxo), ont fait l'objet de plusieurs brevets mettant en évidence leurs propriétés particulières. On peut citer par exemple les brevets français : FR 2.489. 290,2. 489.291, 2.528. 818,2. 621.260, 2.659. 319,2. 666.253, 2.758. 323. En utilisant diverses charges minérales, avec les géopolymères, on a réalisé différents objets décoratifs, comme des objets moulés (statues, bas-reliefs) ou des revtements de sol et de mur comme décrit dans le certificat d'utilité français 2.528. 818. Cependant, la matière finale obtenue ne reproduit pas les caractéristiques d'une pierre naturelle. Plus généralement, la charge minérale a une granulométrie fine, car l'expérience montre que l'emploi de charges de dimension importante (comprise entre 1 mm et 10 mm) s'accompagne irrémédiablement d'un aspect « béton ». En effet, comme il est fait usage de matériaux broyés et sélectionnés, la forme anguleuse des grains ne permet pas d'obtenir une densification optimale, laissant toujours en évidence une zone non cristalline entre les grains.
Au contraire, dans le cadre de la présente invention, on utilise des roches résiduelles naturellement altérées et/ou des roches détritiques, non broyées, permettant de réaliser une pierre dans laquelle on ne voit plus cette zone non cristalline. Dans l'examen optique des lames minces coupées dans les pierres géopolymèriques produites selon l'invention, le pétrographe n'aperçoit en général que les parties cristallines des matériaux d'origine. Le liant géopolymèrique est complètement amorphe, mme à la lumière polarisée, et n'est pas détectable par les moyens conventionnels de microscopie optique.
Exposé de l'invention : L'objet principal de l'invention est de fabriquer une pierre géopolymèrique pour la construction et la décoration, ayant un aspect analogue à de la pierre naturelle. Dans ce qui suit nous utilisons les définitions géologiques et pétrographiques suivantes tirées de l'ouvrage « Précis de Pétrographie » de Jean Yung, Masson et Cie Editeurs, Paris, 1969 : - roche altérée : roche ayant subi une altération superficielle principalement due à l'infiltration des eaux acides (eau de pluie, acides humiques).
-roche résiduelle : l'altération superficielle donne naissance à deux sortes de substances, les unes solides, les autres passées en solution. Les substances solides accumulées sur place forme une roche résiduelle.
- érosion : au contraire de l'altération, phénomène chimique, l'érosion ne met en oeuvre que des processus mécaniques : alternances de sécheresse et d'humiditié et variations brutales de la température, qui entraînent une désagrégation physique des matériaux anciens produisant un arène détritique.
- roche détritique : les arènes détritiques accumulées sur place forme une roche détritique - arkose : variété de grès feldspathique dans laquelle, à coté des grains de quartz, le minéral feldspath se présente en grain dont la taille est analogue à celle des feldspaths du granit d'origine.
- grès à ciment pellitique : à coté des grains de quartz, on trouve de nombreux grains de feldspath, ainsi que des grains microconglomératiques de roches dures, grains composites. Le ciment est fait de poussière de particules de quartz, feldspath, mica, kaolinite.
- arène : dans les régions à climat tempéré, les granites et les grès se transforment communément, par altération superficielle, en une roche sableuse ou en sable, appelée arène. Dans les régions à climat sec et chaud, les roches plutoniques et ignées se transforment par érosion en arène détritique.
- test : coquille, coque, carapace en calcaire de mollusques et de crustacés.
L'objet principal de l'invention est la description de pierres géopolymèriques pour la construction et la décoration, analogue d'aspect à de la pierre naturelle, qui sont constituées de 65 à 95% en poids de roche résiduelle provenant d'une roche naturellement altérée et/ou de roche détritique provenant de l'érosion, et de 5 à 35% en poids de liant géopolymèrique de type poly (sialate), poly (sialate-siloxo) et/ou poly (sialate-disiloxo).
Les pierres géopolymèriques en grès analogue aux roches naturelles appartenant à la classe des grès à ciment siliceux ou des grès à ciment pellitique sont constituées de 65 à 95% en poids d'arène quartziques et/ou feldspathiques, et de 5 à 35% en poids de liant géopolymèrique de type poly (sialate), poly (sialate-siloxo) et/ou poly (sialate-disiloxo).
Les pierres calcaires géopolymèriques de type calcaire à foraminifères, analogues aux roches naturelles appartenant à la classe des calcaires à organismes, sont constituées de
65 à 95% en poids d'un mélange de tests et de sable calcaire, et de 5 à 35% en poids de liant géopolymèrique de type poly (sialate), poly (sialate-siloxo) et/ou poly (sialate-disiloxo).
Parmi les roches à aspect granitique, les pierres géopolymèriques sont de type arkose, c'est à dire analogues aux roches naturelles appartenant à la classe des arkoses. Elles sont constituées de 65 à 95% en poids d'arène granitique et de 5 à 35% en poids de liant géopolymèrique de type poly (sialate), poly (sialate-siloxo) et/ou poly (sialate-disiloxo).
Un second objet de l'invention est la description de pierres géopolymèriques servant de revtement extérieur et/ou intérieur à une âme en béton de ciment Portland et/ou de béton expansé (béton cellulaire).
Le béton cellulaire a les avantages et les qualités suivantes. Les blocs peuvent tre porteurs, isolants, hydrofuges, légers à manier. Le béton cellulaire permet de faire des chantiers propres, car il suffit de mélanger une colle et de monter le mur. Plus besoin de bétonnière, de tas de sable, de ciment Portland avec les problèmes de dosage. Cependant, on a toujours déploré leur fragilité et l'obligation de leur fournir un revtement de finition, après la pause. Pour celle-ci, nous revenons aux problèmes traditionnels du chantier : protection, échafaudages, machine pour projeter, finition manuelle, auxquels s'ajoutent les problèmes liés aux intempéries. Quelles sont les solutions utilisées actuellement. On protège leur surface en collant ou agrafant dessus des briques, des pierres de parement, des carreaux de grès. Ou alors, on projette des enduits hydrofuges dont la durée de vie, pour en conserver un aspect satisfaisant avec la pollution des villes, est de l'ordre de 12 à 15 ans.
On le recouvre aussi de revtements minces s'apparentant à des peintures microporeuses.
Dans aucun cas, le bloc ne se présente dans son aspect de surface fini.
Depuis longtemps on a cherché une finition pouvant tre faite en usine qui permettrait de monter un mur porteur fini et isolé en une seule opération de pose et sans pont thermique. Il ne resterait ainsi qu'au peintre à l'abri des intempéries à enduire et peindre de manière décoratives l'intérieur, l'immeuble étant terminé extérieurement, d'où l'intért de la présente invention comme détaillé ci-dessous. Non seulement la pierre géopolymèrique offre toutes les garanties d'une pierre (calcaire, granit, grès, etc. ) naturelle, mais aussi un aspect final qui peut, par moulage, reprendre n'importe quelle modénature, copie d'ancien ou création contemporaine. Le joint de finition peut également tre fait directement en montant, pour peu que la colle à béton cellulaire soit compatible et légèrement teintée pour l'aspect souhaité.
Meilleures manières de réaliser l'invention Pour réaliser une pierre géopolymèrique selon l'invention on n'utilise pas de préférence de matériaux géologiques broyés mécaniquement en usine, comme c'est traditionnellement le cas dans la fabrication des"marbres artificiels". De préférence, la pierre géopolymèrique selon l'invention est obtenue en utilisant des roches résiduelles et/ou des roches détritiques qui sont employées telles qu'extraites du sol, ou au plus après avoir subit une simple opération de lavage des poussières. De préférence, il n'y a pas de broyage, tout au plus une désagrégation des mottes, pour faciliter le lavage et l'élimination des matières parasites (terre, humus, etc.).
Pour fabriquer une pierre géopolymèrique selon la présente invention on fait durcir un mélange géopolymèrique contenant : a) 65 à 95% en poids de roche résiduelle provenant d'une roche naturellement altérée et/ou de roche détritique provenant de l'érosion ; b) 5 à 35 % en poids d'une résine géopolymèrique d'alumino-silicates de sodium, de potassium et de calcium générant, après durcissement, un liant géopolymèrique de type poly (sialate), poly (sialate-siloxo) et/ou poly (sialate-disiloxo).
Les pierres géopolymèriques de l'invention ainsi que leur procédé de fabrication sont illustrés par les Exemples suivants. Ces exemples n'ont pas de caractère limitatif sur la portée globale de l'invention telle que présentée dans les revendications. Toutes les parties indiquées sont en poids.
Exemple 1 : On utilise une machine employée quotidiennement pour fabriquer des carreaux de marbre artificiel ou de granit artificiel. Cette machine est constituée d'une presse hydraulique dans laquelle on trouve également une table vibrante ainsi qu'une cloche à vide. Les agrégats sont du granit concassé et broyé doté d'une granulométrie optimale afin de laisser le moins de vide entre les grains. La table vibrante permet de placer les grains et la cloche à vide d'éliminer les bulles d'air incluses dans le liant. Pour le marbre artificiel, le liant est une résine organique (acrylique ou polyester) et pour le granit artificiel, le liant est du ciment hydraulique. Au lieu de ces liants traditionnels on utilise maintenant un ciment géopolymèrique de type (K, Ca)-Poly (sialate-siloxo) comme par exemple celui décrit dans le brevet français FR 2 666 253.
On mélange 80 parties d'agrégats avec 18 parties de ciment géopolymèrique et 2 parties de pigment noir. On place le tout dans le moule puis sous la presse vibrante, et on applique le vide. Le carreau comprimé est ensuite laissé à durcir à 60 deg. C pendant 2 heures. Puis on procède à l'opération de finissage qui consiste en un ponçage puis à un polissage. On obtient un carreau de pierre géopolymèrique qui est du granit artificiel, de couleur noire. Dans la structure on distingue nettement entre les grains anguleux une phase amorphe constituée par le ciment et les fines.
Exemple 2 : On fait un mélange contenant 484 parties de granit broyé dont la granulométrie s'étale de 0. 05mm à 7mm, avec 90 parties de ciment géopolymérique (K, Ca)- (poly (sialate-siloxo) et 30 parties d'eau. Ce mélange est introduit dans un moule sous lequel on applique une vibration pour permettre un bon tassement. On fait durcir pendant une journée à la température ambiante et ensuite on démoule. La pierre géopolymèrique est ensuite laissée dans un sac plastique fermé, pendant 1 semaine. On découpe à la scie diamantée. La structure de la pierre est similaire à celle de l'exemple 1 : on distingue nettement entre les grains anguleux une phase amorphe constituée par le ciment et les fines.
Exemple 3 : Dans un gisement de granit fortement altéré où la kaolinisation très avancée donne lieu à une industrie de séparation du kaolin, on choisi une arène granitique qui contient moins de 10% en poids de kaolinite. Cette arène granitique est constituée de grains quartzeux libres, de grains feldspathiques libres, de mica muscovite libre et de kaolinite résiduelle. On fait un mélange contenant 500 parties de cette arène granitique avec 100 parties de ciment géopolymérique (K, Ca)- (poly (sialate-siloxo) et 30 parties d'eau. On fait durcir à 80°C pendant 2 heures et ensuite on démoule. La pierre est ensuite laissée dans un sac plastique fermé, pendant 1 semaine. On découpe à la scie diamantée. La structure de la pierre géopolymèrique est différente de celle des exemples 1 et 2 : on obtient une structure cristalline extrmement dense, chaque grain étant enrobé d'une fine couche amorphe de kaolinite transformée en tecto-alumino-silicate par géopolymérisation. La pierre géopolymèrique obtenue est du type arkose.
Exemple 4 : On procède comme dans l'exemple 3, mais au lieu de prendre l'arène granitique on utilise le résidu d'extraction du kaolin. En effet, lorsque l'arène granitique est riche en kaolin (de l'ordre de 30% en poids par exemple), on extrait ce kaolin par décantation dans l'eau. Les parties lourdes restantes constituent une arène granitique résiduelle contenant au plus 2% en poids de kaolin. On utilise ce résidu comme dans l'exemple 3. La structure de la pierre est différente de celle des exemples 1 et 2 ; elle est similaire à celle de l'exemple 3 ; chaque grain est enrobé avec une très fine couche amorphe de liant géopolymèrique. La pierre obtenue est du type arkose.
Pour fabriquer une pierre géopolymèrique en calcaire on choisira un calcaire à coquillage naturellement altéré. Par exemple pour réaliser un calcaire foraminifère du type nummulite, on fera durcir un mélange contenant 65 à 95% en poids de calcaire naturellement altéré, non broyé, constitué de tests libres et de sable calcaire à tests libres, avec 5 à 35 % en poids d'une résine géopolymèrique d'alumino-silicates de sodium, de potassium et de calcium générant, après durcissement, un liant géopolymèrique de type poly (sialate), poly (sialate-siloxo) et/ou poly (sialate-disiloxo).
Dans le cas des grés à texture fine, on choisira de préférence un gisement d'arène quartzique (ou de sable quartzique) très peu consolidé qui se désagrège aisément par simple pression. L'ajout du ciment géopolymèrique aboutit à la fabrication d'un grès à ciment siliceux ou plus spécialement d'un grès à ciment pellitique.
Les arènes détritiques et les roches détritiques très peu consolidées, par exemple de type basalte et autres roches plutoniques et ignées, permettent l'obtention de pierres naturelles imitant certaines roches métamorphiques.
Les pierres géopolymèriques peuvent tre utilisées comme revtement décoratif ou de protection, en statuaire et autre objet décoratif. Dans la construction elles peuvent servir de revtement extérieur, sous forme de carreaux, de blocs, de briques. On peut également mettre le mélange géopolymèrique en fond de moule et couler dessus soit du béton traditionnel à ciment Portland, soit un béton cellulaire, ou appliquer un bloc de béton dense ou cellulaire déjà durci. L'élément de liaison entre la couche de pierre géopolymèrique et l'âme en béton à ciment Portland dense ou cellulaire est le liant géopolymérique.
Exemple 5 : Le mélange géopolymèrique d'un des exemples précédents 1 à 4 est versé progressivement dans un moule fait soit en plâtre, bois, métal, élastomère, plastique, ou autre, et tassé, vibré afin d'évacuer les bulles d'air. Sur la surface supérieure, où surnage le surplus de liant, est posé le bloc de béton cellulaire, propre et précédemment griffé pour une meilleure adhérence. On vibre et on tasse le tout, sans abîmer le bloc. Puis ont fait durcir la réaction géopolymèrique. Après démoulage, on sable ou on brosse avec une brosse métallique ou on passe le"chemin de fer", selon la finition désirée. Au besoin, et dans certaines conditions, on passera un produit anti-graffiti transparent. On obtient ainsi un bloc de pierre d'aspect naturel à l'extérieur et isolant à l'intérieur. Pour accélérer la prise, l'opération de pose du béton cellulaire sur le surplus de liant peut se faire à la sortie de l'autoclave, le bloc encore chaud.
Au lieu de bloc de béton denses ou de béton cellulaire, déjà durci, on peut aussi couler sur la surface du mélange géopolymèrique, du béton frais de ciment Portland ou un béton cellulaire prt à l'expansion. Le durcissement de l'âme de béton en ciment Portland se fait dans les mmes conditions que celui de la pierre géopolymèrique.
Par ailleurs, dans le but d'une meilleure intégration de la construction dans le cadre bâti local, sachant que l'on trouve des roches résiduelles ou des roches détriques dans presque toutes les régions, le choix se portera sur la plus proche d'aspect de l'architecture traditionnelle locale.
Bien entendu, diverses modifications peuvent tre apportées par l'homme de l'art aux méthodes et aux pierres géopolymèriques qui viennent d'tre décrites uniquement à titre d'exemple, sans sortir du cadre de l'invention.
l'hiver est passé, propice aux recherches et expérimentation sur le sujet.
Las d'essayer avec mon argile peu réactive, j'ai acquis une palette d'argical 1200s ( une palette de 900kg) chez ags minéraux.
L'argical 1200s est un kaolin cuit à 750 ° autrement nommé méta kaolin et a son équivalent naturelle: la pouzzolane. Cette cuisson lui confère des propriétés réactives tant avec les ciments portland que la chaux et bien sur les alcalins comme les solution l'hydroxyde de potassium (KOH) ou de sodium(NAOH avec un silicate de sodium(Na2SI03) ou potassium (K2SI2O5).
Pour les ciment:
Il peut remplacer jusqu'à 20% de la masse de ciment nécessaire, il réagit avec la chaux libre inévitablement présente dans le ciment ce qui accroit les performances mécanique et la résistance aux agressions chimiques. Il agit aussi comme accélérateur de prise.
Pour la chaux:
Mélangé à hauteur de 20% en poids avec la chaux il réagit avec celle ci , cette réaction pouzzolanique est bien connue et utilisée depuis l'antiquité notamment chez les Romain. Le méta kaolin remplacerait avec avantage le ciment ajouté pour la pierre reconstitué classique.
Avec les solution alcaline:
C'est le sujet qui m'intéresse le plus,
La littérature est importante sur le sujet, les résultats converge le tout est d'interpréter cette masse d'information.
- les facteurs influent sur le résultat final
Le rapport SI/AL globale
le rapport (NA,K)OH/eau
la température de cuisson( de température ambiante à 80°)
le temps de malaxage
l'agrégat utilisé ( le sable donnera un matériaux plus résistant que le calcaire)
Mise en œuvre:
proportion
Pour 10000 g de calcaire en poudre 0/2 il faut:
3000 g d'argical
600g de Koh ou NAoh à 10m/l ( 1mole de naoh = 40g et 1 mol de koh = 56g) soit
900 g de silicate
1 à deux litre d'eau suivant l'état de sècheresse de l'agrégat Je conseille les plastifiants et superplastfiant, à tout ceux qui ont des problèmes de trop d'eau pour leur mélange traditionnels
Les essais que j'ai fait sans donne un résultat moyen, il y à toujours trop d'eau et la propriété colle de l'argical empêche un mélange homogène
Gâchage:
dissoudre le koh ou naoh avec la quantité d'eau adéquat ( attention ça chauffe très fort et c'est très agressif)
attendre le refroidissement et ajouter le silicate, , le superplastifiant ( certain dise qu'il faut ajouter à ce moment l'eau additionel mais pour moi c'est trop tôt)
laisser reposer 1/4 h le temps de mélanger à sec l'agrégat et l'argical
Ensuite, le mélange n'est pas vraiment possible à la bétonnière il faut un mélangeur au bout d'une perceuse dans un cuve de gachage ( ronde de préférence) ou mieux un malaxeur , mettre le liquide refroidi dans la cuve,( attention au projection, porter des gants) et verser progressivement le produit sec tout en mélangeant.
Si le mélange ne devient plus possible, c'est très très collant!! Rajouter de l'eau.
Il faut bien mélanger de manière à obtenir un mélange homogène.
Vous avez ensuite en gros deux heures pour faire votre coulée.
Remplire votre moule bien tasser l'ensemble (pas facile) l'idéal c'est une table vibrante, le produit qui est très visqueux à tendance à faire beacoup de bulle ( ce qui est un avantage contre le gel, mais un incovénient pour les usinages et finition.
couvrir le tout avec un sac plastique.
Suivant la température la prise varie entre 1 heure (60°) et 12 heures (20°) pour la prise à température ambiante. Dans tous les cas la prise doit se faire sous atmosphère humide, c'est la raison du sac plastique il faudrait éviter aussi les moule en bois qui absorbe l'eau ou alors les recouvrir d'une couche de résine.
La mise en température est vivement recommandé pour des résistances de l'ordre de 90 mpa, à température ambiante on obtient une résistance approximative de 40 mpa.
Contrairement au ciment qui atteint sa résistance maxi à 27 jours, la résistance est atteinte dans les premières heures
Si vous avez pu utiliser une étuve vous pouvez démouler au bout d'une heure et 4 à 4 à 5 heures dans le cas contraire.
Résultat.
La pierre résultante est une vraie pierre.
Suivant les conditions de préparation elle peut être semblable à une céramique ( brillant et lisse) ou d'aspect mat.
l'argical par sa couleur blanche légèrement rosé et sa très grande finesse donne une pierre blanche du genre de la craie ( au début elle est grise)
Si vous avez des question n'hésitez pas, il y tellement de chose à dire
Très très instructif ton topic ! et très au coeur de la matière minérale ...
Merci de continuer à nous donner tes réflexions sur le sujet et tes résultats d'expérience.
Merlin
Sans aller jusqu'au procédé ultime, le remplacement du ciment par le métakaolin serait sans aucun doute bénéfique pour les pierres reconstituées car chacun sait que les ciments modernes ne teindrons pas aussi longtemps que le viaduc du Gard ou le Colisé.
j ai besoin de votre aide à propos d un sujet de géopolymère
voila je fais un stage sur les géopolymères, j'utilise du kaolin comme argile, donc ma premiere fabrication de géopolymère sera à partir du kaolin sec et du NaOH tout en respectant le rapport molaire Si/Al = [n(Nao2)/n(Al2o3)] =1, à partir de ce rapport, de la formule du kaolin et du fait que n(Nao2)+n(Al2O3) = n(kaolin) je dois trouver la masse de NaOH que je dois ajouter au kaolin pour fabriquer le géopolymère, j ai essayé mais je suis pas arrivé au bon résultat.
merci de votre compréhension et de votre aide
quelque chose comme 8% de na2O (plutot que na02)
il me semble qu'avec na02 tu as du manquer d'ion OH
le kaolin :
Al2O3·2SiO2·2H2O
vous avez
MM SI02 = 60,08
MM NA20 = 61,979
MM H20 = 18,052
MM AL2O3 = 101,961
MM NAOH = 40
2NAOH + SIO2 ---> donne normalement en condition de température adéquate du NA2 SI03+ H2O ou NA2O + SIO2 + H2O
SiO2/Al2O3 (S/A) = 1 dans votre cas ( un kaolin bien pauvre en SI)
Na2O/Al2O3 (N/A) = 1
(Nao2)+(Al2O3) = Al2O3·2SiO2·2H2O
ou plutot
na2O ?
ce qui ne fait qu'un ensemble d'équation à résoudre, la seule inconnu état naO2 (na2o?)
Bonjour,
Tout d'abord, merci pour un site web merveilleux qui trait un question qui me tracasse depuis des décennies... rien de ce type n'existe ailleurs (à ma connaissance).
Suivant les conditions de préparation elle peut être semblable à une céramique ( brillant et lisse)
C'est le but qui m'a amené ici: fabriquer des dalles/carrelages polissable pour cuisine qui ont un aspect pierre.
Jusqu'au présente, mes recherches et reflexions sur ce sujet m'amèner a concevoir un systeme de moulage de dalle/carreau 'deux couches': un premiere couche (surface, du fond dans la moule) qui contient les matières de pierre naturelles, et le reste de l'epaisseur dans un couche plus épais de ciment (avec peut-etre fibre).
Mais c'est ce première couche de pierre naturelle reconstitué qui me pose question: comment le rendre assez dur pour resister au usage, avec un surface lisse et polissable?
Melanger le calcaire broyé (dure, de bourgogne de preference) avec le meme mesure de poudre de quartz me semble etre un bonne idée (pour mon cerveau naif non-experimenté dans ce domaine)... et je suis en train de jouer avec l'idée de utiliser un liante synthetique comme indiqué dans l'extrait d'article publié par Roseau (merci!) au lieu de ciment.
Bien sur je partagerai les resultats de mes essais ici, mais avant de m'y lancer, j''aimerais avoir l'avis de ceux (vous!) qui sont plus expérimenté que moi.
Merci d'avance pour tout critique/commentaire!
Mais suivent le sujet de ce conversation, je me demande s'il est possible de faire un melange qui est 'plus vrai que le nature' (avec des aspect 'naturelles'): de simuler un calcaire 'dur'? Je ne suis pas si avancé en chimie pour cela, helas, mais peut-etre en étudiant le composition du calcaire dur, on peut arriver a créer un melange des composites semblables au ceux deposées par la nature.
Bonjour ThePromenader,
Votre projet est très intéressant. Mettre au point une solution pour obtenir de la pierre calcaire "géopolymère" très dure avec des moyens simples et des éléments naturels courants serait du plus grand intérêt pour les amateurs. Je n'ai pas les connaissances pour vous aider, mais j'espère que des spécialistes du domaine, comme Roseau, passeront par là.
Dans tous les cas, je suivrai avec grand intérêt les résultats de vos essais.
Loup
Merci, Loup. Oh, et j'ai oublié à dire: je suis d'origine anglophone, donc desolé d'avance pour les fautes d'orthographe et grammaire que vais sans doute faire.
Aprés quelques recherches, j'apprends déjà que les calcaires 'durs' sont plus fort en silice (sable?) et non de quartz, mais les composents liantes resetent le meme. Je me demande, toutefois, si un peu de quartz donnera l'aspect 'brilliante' que je recherche (le silice a tendence d'être, au mieux, plutot 'matte' et 'happe' quand il est sèche et non-traité... et il s'impregne assez facilement avec l'eau).
Et j'apprends que le calcaire métamorphosé est du... marbre. Interessante (car je pense a ajouter un peu de farine de marbre à la melange pour la finesse du finition).
PS: J'ai regardé aussi le pierre bleue (un calcaire non-métamorphosé tres dur, compacte et TRES polissable) pour rester dans les calcaires 'purs'. Un article d'un université Belge donne le composition suivante:
Composant
Formule chimique
Pourcentage (%)
Carbonate de calcium
93-98
Carbonate de magnésium
1-10
Silice
SiO2
2
Pyrite
FeS2
0,5-1,5
Carbone
<0,5
Argile
-
0,1
Séricite, zircon, rutile, tourmaline, fluorine
-
Traces
Caractéristique
Unité
V aleur(a)
Masse volumique apparente
kg/m3
2.687
Porosité (vide de 98,66 kPa)
0,28
Résistance à la compression
157,9
Résistance à la flexion
16,7
Vitesse du son
m/s
5.527
Module d'élasticité statique
86.900
Usure
2,87
Dilatation thermique
mm/mK
0,0046
(a) Valeur moyenne des résultats d’essai
(Desolé pour le grande espaces en haut des tables, mais c'est votre 'formatage' du forum qui l'insére; quand-meme, j'ai essayé tout pour les enlever)
Peut-etre avais-je tort de commencer ce sujet ici je voulez parler de 'reconstitution' aussi, mais ca devient autre chose... si vous voulez le bouger dans un conversation nouvelle, je vous en prie, faites-le.
Mais selon le charte ci-haute, je peux conclure que le 'durété' et brilliance d'un pierre (composite) est du pas seulement par son composition chimique, mais par sa porosité.
Il faut donc un concassage de calcaire très fin, sinon il faut remplir les 'trous' entre-granules avec les autres composents... mais un granularité 'large' se usera plus rapidement que le 'ciment' qui l'entoure, n'est-ce pas? Il faut donc un grain de calcite tres fin.
Il faut aussi eliminer toute bulle d'air present dans le melange. En lisent l'article fourni par Roseau, je pense d'avoir trouvé un alternatif à leur solution d'utiliser un table de vibration... faire le plus grande vibration dans le bac de melange; il faut peut-être un vibration supplimentaire apres avoir versé le melange dans le moule, mais au moins ce sera moins important (et demandera moins d'équipement) que leur methode.
Je crois qu'il faut mettre un pression aussi (comme le technique utlisé pour le fabrication des carreaux de ciment), mais peut-etre un technique de 'sous-vide' de moule suffira.
Ce sont que mes pensées; je n'ai jamais essayé un chose semblable jusqu'au présent.
Et il y a ça, aussi:
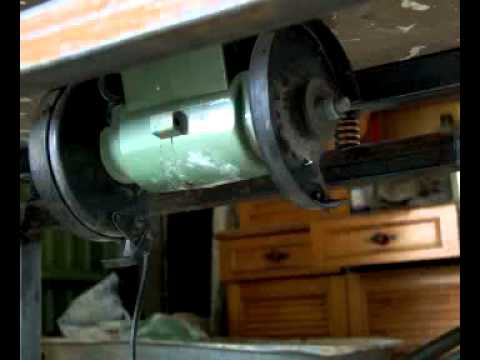
Research update:
Il me semble que les liantes synthétiques pour un reconstitution de pierre destinée pour le sol sont... pas trés bien, car pas seulement ils n'aurient pas 'l'eclat' des pierres natureles, mais les polymeres riquent à 'bruler' sous l'effet du polissage (sauf si on utilise des produits qui sont leur destinées).
Cela devient un vraie défi.
Le vibration semble être le meilleur facon d'arriver a une densité, sans bulles d'air, acceptable.
Le melange 'ideale' que je vois au present (avec mes connaissances limités), pour les agrégats de couche 'surface' en tout cas, c'est un melange de 60% calcaire (broyé -tres- fin), 20% de quartz, 10% de farine de marbre et 10% de silice.
Je regarde toujours pour le carbonate de magnésium... j'avais pensé que c'est le produit du mortier/ciment qui à 'pris', sèchée, mais non. Peut-etre faut-il remplacer le farine du marbre par ceux-ci (il est disponible au prix raisonable dans les magasins du sport).
Pour le moment, je suis à un impasse complet sur le question de quel liant utiliser/concocter.
!!!
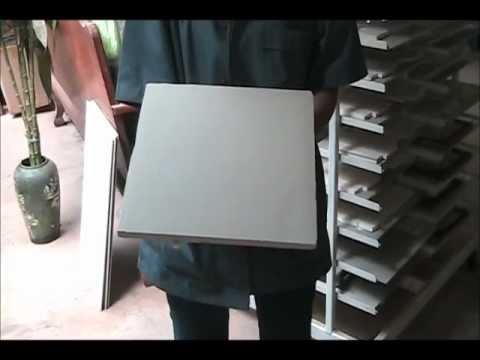
Conclusion:
Pour le liante, le melange 20% métakaolin-80% ciment semble être meilleur solution pour garder un aspect 'pierre dur' durable.
Par ce que je peux comprendre, le plus fin le granularité, le plus 'fin' le résultat. Avec un moule convenable, poli aspect 'miroir', avec un melange avec un granularité extrêmement fin, il est meme possible d'avoir un plaque/dalle/carreau avec un aspect 'émail', mais ce n'est pas toute-à-faite le but ici.
Pour créer un 'pierre de Bourgogne polissable', je compte créer un melange des agrégats qui sont:
85% de Carbonate de Calcium (de preference calcaire de Bourgogne broyé tres fin)
8% de Quartz
5% de Carbonate de magnésium (qui remplace le farine de Marbre dans mon idée initiale)
2% de Silice
Tout avec un granularité le plus fin que possible, bien sur.
Il faut aussi un melange pauvre en eau qui peut être 'vibré' de tout bulle d'air et pour obtenir un densité extreme, donc je pense ajouter un superplastifiante (pas trop!) au melange metakaoline-mortier, créer un moule 'fond plat' lisse qui peut être vibré (le verre ne supporterai pas cela, donc de plexi), et j'ai déjà fabriqué un 'vibreur' (un boulon décentré vissé entre deux autres sur un écrou tenu par un perceuse; le corps de perceuse est appuyé contre le fond du moule). Je pense aussi que le metakaolin sert de 'impermeabilisateur', mais j'ajouterai de hydrofuge s'il est nécessaire.
Je -pense- que avec cela j'aurai un roche dense, grain fin, qui peut-être poli... ce sera que le surface de dalle (8-10mm d'un dalle épais de deux centimetres), et le reste d'épaisseur sera de ciment 'traditionnel' (mélange peut-être avec un peu de fibre).
Je vous enverrai les résultats quand j'aurais le temps (et la place!) de faire un essai (dans deux semaines environ).
En attendant, toute critique et commentaire sera le bienvenue - c'est le premiere fois de ma vie que j'entreprend un tel projet!
bonjour,
les geopolymers ne sont pas des polymers plastique mais minéraux et ne sont pas influencé par le polissage
ceci étant le geopolymer est difficile a mettre en oeuvre, pour des particuliers, avec les éléments que j'ai indiqué.
Par contre, un mortier a base de chaux aerienne, de metakaolin (genre argical 1200s) vous donnera un liant de très bonne qualité, c'est avec ce type de mortier que sont fait les monuments romain
Pour le ciment portland on peut le remplacer a hauteur d'1/3 par du métakaolin qui ne joue pas le role d'imperméabilisant mais de réactif
attention quand même à la granulometrie, trop fin ce n'est pas forcément gage de dureté!!
Merci Roseau,
Merci beacoup de vos conseils. J'attends l'accord du propriétaire (je suis locataire) pour mes renovations (les dalles font qu'un parti), mais je crois que cela debutera dans quelques semaines. Je vous tienderai au courant dans le rubrique 'chantier'.
Un p'tit question: qu'est-ce que vous conseillerez pour obtenir un pierre dur, genre 'traffic intense'?
Encore merci!
Bonjour à tous, tout d'abords merci d'avoir validé mon inscription sur le forum et en espérant ne pas avoir raté un sujet "présentation" je fais remonter ce fil de discussion dans l'idée d'encourager d'éventuels retour d'expérience ou susciter des commentaires/vocations/essais.
Mon objectif, un peu comme tous ici, est d'imiter la pierre et dans mon cas des pierres de couverture extérieure, finition lisse, couleurs hétérogènes, d'aspect mat. Les essais aux "bétons" (adjuvantés, fibrés, colorés) donnent des résultats, mais l'aspect trop fin (lisse et brillant) des peaux de béton et l'impossibilité de faire une retouche de "taille" (un coup de ciseau fait apparaitre la matrice du béton qui trahi son origine) me conduit à envisager les geopolymères.
La technique est depuis quelques années en voie de maturation, j'en veux pour preuve les travaux publiés à ce sujet comme ici : https://tel.archives-ouvertes.fr/tel-01297848/ une thèse entière y est consacrée. Et le métakaolin est maintenant disponible assez facilement pour le particulier (sous le nom d'Argical 1000 et 1200) avec d'ailleurs les réactifs nécessaires aux formulations.
Voilà, si ce post appelle quelques commentaires je les lirai avec plaisir.
Cordialement.
Bonjour,
C’est un peu vieux mais je reprend mes activités de mouleur , après une période de tailleur de pierre
En quelques années la littérature sur le sujet a été décuplée
J’ai fait quelques essais supplémentaires avec la poudre résiduelle de la taille le résultat est là , avec les bons dosages de métakaolin, de soude, de silicate, d’eau et d’agregat un passage au malaxeur et au vibreur et le résultat est sans commune mesure avec un ciment, et ceci sans compromis sur les propriétés mécanique.
Il y a même des fabricants qui proposent les produits ( Metakaolin, + activateur).
Par ailleurs le metakaolin ajouté à de la chaux aérienne ( 1volume de chaux , 1 volume de meta ) 2 volume d’agrégat , de l’eau sans abuser, un passage au malaxeur et vous avez une pierre d’un aspect magnifique qui va prendre dans le même temps qu’un ciment, vous pouvez faire les assises les joints etc.
Bonjour,
j'ai fait quelques travaux cet été , dont un peu de moulage geopolymère.
je joins un photo
La couleur est très rouge du fait de la forte proportion d'argile, mais la réaction chimique fait migrer les oxydes de fer en surface et après quelques temps il seront lavés. Au bout de 12 h il faut un disque diamant pour l'attaquer
bonjour,
je joins une photo du moulage dans son environnement ( à gauche) , j'ai fini les joints de dallage , ( chaux aérienne , métakaolin , sable)
reste à brosser les dalles pour enlever le surplus de joint et à laver le moulage pour faire disparaitre les efflorescences
sinon sous la bache verte qui protège la grue il y a la dalle du puit
avant
après
je doit encore mouler les pierres de la margelle, j'ai le moule reste plus qu'a s'y mettre
Bien le bonjour les amateurs de pierres.
Je suis ce sujet depuis quelques années avec beaucoup d'intérêt, il était en favori dans mon navigateur, et aujourd'hui je décide de me lancer.
J'habite le Brésil et ici il n'y a pas cette tradition de travail de la pierre.
J'ai réussi à me procurer l'hydroxyde d'aluminium et du calcaire broyé extrêmement fin, blanc, utilisé dans l'agriculture pour alcaliniser les sols (malheureusement impossible de trouver sous forme de sable).
J'ai quelques doutes au sujet des autres produits. Les poids indiqués sont ils pour des produits secs ou en solution aqueuse (hydroxyde de sodium et soude)?
Je ne sais pas en France, mais ici le silicate de sodium est extrêmement cher, rendant cette technique peu viable. Je me lance plus par passion.
Je me contenterai certainement du metakaolin comme additif à la chaux.
En tous cas un grand merci à Roseau pour ces retours d'expérience.
Bonjour ,
l'hydroxyde d'aluminium je ne voix pas pourquoi!!
le silicate de soude est titré à 39 % c'est un liquide liquide en fance 66 euro les 20 l
metakaolin mk 750 --> poudre --> attention aux differentes compositions qui donnent des résultats différents ( plus ou moins de silicium et d'aluminium)
hydroxide de sodium( soude) en granule , paillette ou autre
Attention au mélange, de la chaux , métakaolin et agrégat, c'est très très sensible à l'eau, un malaxeur s'impose pour obtenir un mélange homogène avec un minimum d'eau car le produit très collant.
Tu n'as pas plus de 4 heures pour travailler le mélange après ce n'est plus vraiment utilisable